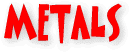
PROPERTIES OF METALS
- Metals are elements that have atoms arranged in rows. The electrons are easily released from metal atoms so that layers of metal atoms exist in a 'sea' of electrons.
- Examples of Metals are gold, copper, lead, zinc, iron, magnesium, sodium, calcium and mercury.
- Physical Properties of Metals include shiny lustre, greyish - silver colour, hardness, good heat and electricity conductivity, high melting and boiling points, malleability (can be hammered into a sheet) and ductility (can be pulled into a wire).
Some exceptions to these are the metals - sodium and calcium (very soft), gold and copper (yellowish colour), and mercury (low melting and boiling points).
- Chemical Properties of Metals
Some metals are more reactive than others. This is because very reactive metals lose electrons easily. Metals such as sodium are very reactive and are explosive in air. Metals such as gold are very unreactive, and therefore do not corrode or tarnish in air.
CHEMICAL REACTIONS OF METALS
- 3 Chemical Reactions of Metals
- Metal + Acid
Salt + Hydrogen
- Metal + Oxygen
Metal Oxide
- Metal+Water
Metal Hydroxide + Hydrogen
- Activity Series of Metals lists metals from the most reactive (e.g. potassium and sodium) to the least reactive (e.g. gold).
Potassium - K |
Most Reactive |
Sodium - Na |
Calcium - Ca |
Magnesium - Mg |
Aluminium - Al |

|
Zinc - Zn |
Iron - Fe |
Tin - Sn |
Lead - Pb |
Least Reactive |
Copper - Cu |
Silver - Ag |
Gold - Au |
- Corrosion is the process that occurs when a metal reacts with air, water or other substances in its surroundings.
- Examples of Corrosion include the rusting of iron in oxygen to form iron oxide, and the green tarnish on copper.
- 4 Ways to Prevent Corrosion:
- Painting - to prevent contact between the metal and oxygen
- Coating with Plastic, Oil, Grease or Tar - to prevent oxygen contact with the metal
- Coating with Metal - Galvanising iron with zinc
- Sacrificial Protection - enclosing a metal to be protected with a more reactive metal which will corrode first
ALLOYS
- Alloys are mixtures of metals with either other metals or with non-metals such as carbon and silicon. This is done to develop lighter, stronger or corrosion-resistant metal alloys.
NAME OF ALLOY |
PERCENTAGE OF EACH METAL |
Bronze |
Copper (92%), tin (6%), zinc (2%) |
Brass |
Copper (70%), zinc (30%) |
Steel |
Iron (99%), carbon (1%) |
Stainless steel |
Iron (75%), carbon (1%), chromium (20%), nickel (5%) |
Duralium |
Aluminium (95%), copper (4%), manganese (1%) |
Magnalium |
Aluminium (70%), magnesium (30%) |
Type metal |
Lead (72%), antimony (18%), tin (10%) |
Solder |
Lead (50%), tin (50%) |
Pewter |
Tin (85%), copper (7%), bismuth (6%), antimony (2%) |
Sterling silver |
Silver (92.5%), copper (7.5%) |
22 carat gold |
Gold (92%), silver (4.9%), copper (3.1%) |
18 carat gold |
Gold (75%), silver (15%), copper (10%) |
MINING AND MINERALS
- Open - Cut Mining involves digging a huge hole in the ground (e.g. iron, copper, uranium)
- Shaft Mining involves mining in tunnels (e.g. coal, gemstones)
- Dredging involves mixing large amounts of water with the crushed ore to allow the heavier minerals to settle to the bottom (e.g. tin, mineral sands)
- Some Important Mining Terms:
- Metal - the element within a mineral (e.g. iron)
- Mineral - the compound of a metal in combination with other elements such as oxygen (e.g. haematite FeO)
- Ore - a large deposit of a mineral which is economically viable to mine and refine (e.g. iron ore or haematite)
- Gangue - the waste material of an ore from the crushing process
- Some Common Metals and their Minerals:
- Aluminium - Bauxite
- Copper - Chalcopyrite
- Iron - Haematite
- Lead - Galena
- Tin - Cassiterite
- Titanium - Rutile and Ilmenite
- Zinc - Sphalerite
REFINING METALS
- After the ore has been mined, the metal has to be extracted or refined from the mineral. There are 2 main refining processes - smelting and electrolysis.
- Smelting in a Blast Furnace
A blast furnace is a huge oven where minerals may be first roasted to form a metal oxide and then reacted with coke (a purer form of coal containing carbon) to extract the refined metal. Often limestone is added to the blast furnace to help in the removal of impurities which are called slag.
Smelting - Example 1
- In the smelting process to extract lead from its mineral ore (Galena PbS), the galena is first roasted or reacted with oxygen to remove the sulphur.
- Lead Sulphide (Galena) + Oxygen
Lead Oxide + Sulphur Dioxide
- PbS + O2
PbO + SO2
- Then the lead oxide is reacted with the carbon in coke to obtain the refined lead.
- Lead Oxide + Carbon
Lead + Carbon Dioxide
- PbO + C
Pb + CO2
Smelting - Example 2
- In the smelting process to extract iron from its mineral ore (Haematite Fe O), the iron ore undergoes a series of reactions in the blast furnace. Again, carbon is in the form of coke. Also, limestone is added to remove the slag.
- Heat comes from hot air forced into the furnace. The molten iron collects at the bottom of the furnace where it is tapped off.
- Carbon + Oxygen
Carbon Monoxide
- C + O2
CO
- Iron Oxide + Carbon Monoxide
Iron + Carbon Dioxide
- FeO + CO
Fe + CO2
- Electrolysis
Electrolysis is used to extract more reactive metals such as sodium and aluminium. An electric current is passed through a solution (e.g. seawater) or a molten liquid (e.g. molten alumina Al2O3).
For example, sodium chloride in seawater is placed in a container with two carbon electrodes. An electric current is passed through the liquid. The sodium metal ions which are positive are attracted to the negatively-charged electrode (cathode). The negative chlorine ions are attracted to the positively-charged electrode (anode) and chlorine gas bubbles off.
|
|